To check whether the precision of vacuum cleaner parts complies with regulations, manufacturers need to establish a robust quality control and testing process. The specific regulations may vary by region or market, so it's essential to be aware of the applicable standards and requirements. Here's a general guide on how to ensure compliance:
1. Understand Regulatory Requirements:
Familiarize yourself with the relevant regulations and standards governing vacuum cleaner parts in your target markets. In the United States, for example, the U.S. Environmental Protection Agency (EPA) may have regulations related to vacuum cleaner performance and emissions.
2. Documentation and RecordKeeping:
Maintain thorough documentation of the manufacturing process, including design specifications, quality control procedures, and testing protocols. Keep records of all production steps and inspections.
3. Quality Control Plan:
Develop a comprehensive quality control plan that outlines the specific criteria, tolerances, and testing methods required to ensure compliance with regulations. The plan should include checks for dimensional accuracy, material quality, and performance characteristics.
4. Measurement and Inspection:
Utilize precise measuring equipment, such as calipers, micrometers, and gauges, to measure critical dimensions of the vacuum cleaner parts. Conduct regular inspections during and after production to verify compliance.
5. Sampling and Testing:
Determine appropriate sampling procedures based on regulations and standards. This may involve random sampling or 100% inspection, depending on the criticality of the parts.
Conduct relevant performance tests, such as airflow measurements, pressure drop tests, or emissions testing, as specified by the regulations.
6. Metrology Equipment:
Invest in advanced metrology equipment like Coordinate Measuring Machines (CMMs) or optical measurement systems to perform precise and accurate measurements, especially for critical dimensions.
7. ThirdParty Testing:
Consider working with accredited thirdparty testing laboratories that specialize in vacuum cleaner parts. Thirdparty testing can provide independent verification of compliance with regulations.
8. Traceability:
Implement a traceability system that allows you to track each part back to its production batch, supplier, and manufacturing process. This is crucial for accountability and recalls, if necessary.
9. Audits and Inspections:
Conduct regular internal audits and inspections to ensure that quality control procedures are followed correctly. Address any noncompliance issues promptly.
10. Supplier Quality:
If you source components or materials from suppliers, ensure that they also adhere to quality control processes and provide the necessary certifications and documentation.
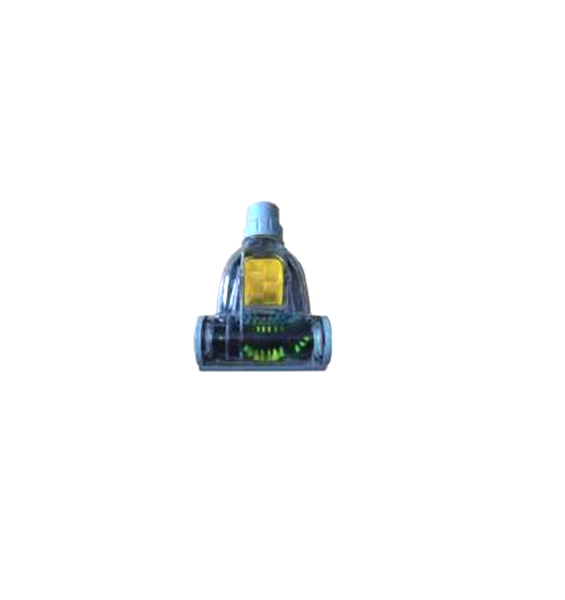
11. Regulatory Certifications:
Seek certification from relevant regulatory bodies or agencies that oversee compliance with vacuum cleaner regulations. This may include certifications like ENERGY STAR or compliance with specific emissions standards.
12. Continuous Improvement:
Establish a culture of continuous improvement, where feedback from testing and inspections is used to identify and address areas for enhancement in both design and manufacturing processes.
13. Documentation Review:
Review your documentation and testing data regularly to ensure that any deviations or issues are promptly addressed and corrected.
14. Market Surveillance:
Stay informed about changes in regulations and market requirements. Continuously update your quality control processes and testing procedures to remain compliant.
By implementing these steps, can establish a comprehensive quality control and testing process that ensures the precision of vacuum cleaner parts and verifies their compliance with applicable regulations and standards.